ISO12100 機械安全
このページでは「ISO12100」についてご説明します。
- 目次
- 概要
- リスクアセスメント
- リスク低減の3段階アプローチ
- 機械のライフサイクル全体でのリスクアセスメント
- ユーザーインターフェースと緊急停止装置
- 文書化と継続的改善
- まとめ
1.概要
ISO 12100は機械類の安全性に関する国際規格です。正式な英名は“Safety of machinery – General principles for design – Risk assessment and risk reduction”であり、JISではJIS B 9700「機械類の安全性−設計のための一般原則−リスクアセスメント及びリスク低減」が対応しています。この規格は、機械のリスクアセスメントとリスク低減に関する包括的なガイドラインを提供することを目的とし、設計者や製造者が安全な機械を作るために従うべきプロセスを示しています。以前はISO 12100-1とISO 12100-2に分かれていましたが、これらを統合して2010年に発行されました。ISO 12100-1とISO 12100-2の内容を一本化することで、規格の使用がシンプルになり、設計者や製造者が機械安全に関する手順をより効率的に実行できるようになっています。
2.リスクアセスメント
ISO 12100は、リスクアセスメントを中心に機械の安全性を確保するプロセスを明確に定義しています。リスクアセスメントは以下の4つのステップで体系化されています。
2.1. 機械類の制限の決定
リスクアセスメントの最初のステップは「機械類の制限の決定」です。ここでは、機械の使用目的や機能、操作環境、機械の寿命などを具体的に定義します。このステップは、リスク評価の範囲を正確に把握し、後続のリスク特定や低減策の検討を効率的に行うための基盤を作る重要なプロセスです。
- 使用上の制限:機械を誰が何のために使用するか、どのような作業を行うかを明確にし、使用を制限します。
- 空間上の制限:機械の大きさや可動範囲、想定している使用環境などから、どのような空間で使用されるかを制限します。
- 時間上の制限:機械本体や機械に備わる各要素(工具やベアリング、電気絶縁性能など)の寿命を明確にし、使用を制限します。
2.2. 危険源の同定
「機械類の制限の決定」が終わった後は、「危険源の同定」を行います。このステップでは、機械の全ライフサイクルにわたって考えられる潜在的な危険源をリストアップします。
- 危険源の分類:機械的、電気的、熱的、化学的なリスクのほか、人間工学的な要因や動力源による危険などを含めて分類します。
- 使用シナリオごとの分析:正常な運転時だけでなく、保守作業や非常時の操作などのシナリオを考慮します。
- 予測される誤操作:使用者の誤操作が引き起こす危険も考慮し、適切な保護策を検討します。
2.3. リスク見積り
リスク見積りは、特定された危険源に対するリスクの大きさを評価するステップです。ここでは、リスクの発生確率とその結果の重篤度を定量的または定性的に評価します。
- 発生確率の評価:リスクが発生する可能性がどの程度かを見積もります(頻度や条件によって分類)。
- 結果の重篤度の評価:発生した場合の影響がどの程度重大かを見積もります(軽傷から致命的な傷害まで)。
- リスクレベルの決定:発生確率と重篤度の組み合わせによってリスクレベル(高・中・低)を決定します。
2.4. リスクの評価
リスクの評価は、リスク見積りの結果に基づいて、リスクが許容可能かどうかを判断するプロセスです。リスクレベルが許容範囲を超えている場合、リスク低減策を講じる必要があります。
- リスクの許容基準の設定:どのリスクレベルが受け入れられるか、基準を定めます(法規制や業界標準に従うことが多い)。
- リスクの優先順位付け:リスク低減策を講じるために、どのリスクから対策を行うべきかを決定します。
- 低減策の決定:リスクが許容できない場合、設計変更や保護措置、警告表示などのリスク低減策を検討・実施します。
以上の4つのステップにより、リスクアセスメントは機械の安全性を確保するための体系的なプロセスとして実施されます。それぞれの段階で適切な対応を行うことで、事故の予防や安全対策の強化が可能になります。図で表すと以下のようになります。
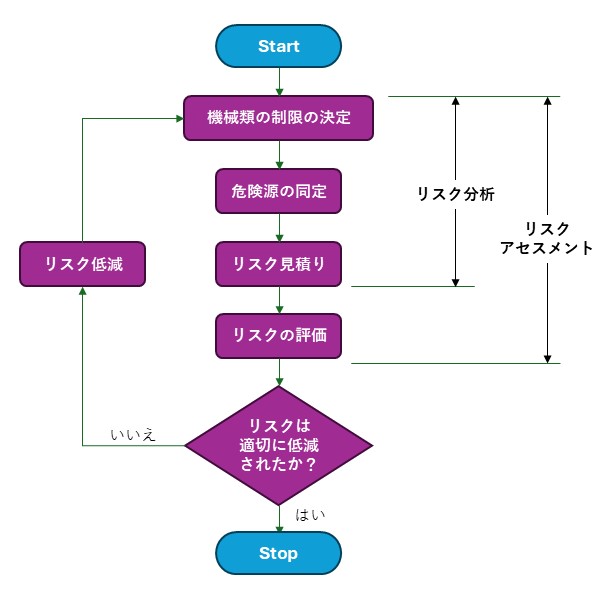
3.リスク低減の3段階アプローチ
ISO 12100はリスク低減に関して、以下の3段階アプローチを提唱しています。このアプローチはリスクを段階的に低減する方法で、できる限りリスクを低減するための順序を明確にしています。
- 本質的安全設計方策(設計による安全化):最も優先すべきは、設計の段階で危険源を取り除くことです。たとえば、部品の形状を変更して鋭利なエッジをなくしたり、自動停止機能を追加することで安全性を高めたりします。設計段階でリスクを取り除くことができれば、後から保護装置を追加する必要がなくなるため、最も効果的なリスク低減策となります。
- 安全防護策及び付加保護方策:設計による安全化でリスクが十分に低減できない場合、物理的な保護措置を導入します。具体的には、安全ガードやバリアの設置、光電センサーや安全スイッチの使用によって危険区域へのアクセスを制限したり、異常が検出された場合に自動的に機械を停止するようにします。
- 使用上の情報(警告表示および使用者への情報提供):残存リスクが完全に排除できない場合は、使用者に対してリスクについての情報を提供します。安全マニュアルや警告ラベル、指示表示などを通じて、正しい操作方法や緊急時の対応方法について周知する必要があります。また、個人用保護具(PPE)の使用を推奨する場合もあります。
4.機械のライフサイクル全体でのリスクアセスメント
ISO 12100は、機械の全ライフサイクル(設計、製造、据付、運転、保守、廃棄)を通じてリスクアセスメントを行うことを求めています。各段階においてリスクを評価し、それに応じた低減策を講じることが重要です。
- 設計段階:この段階ではリスクを予防するための最初のアプローチを行います。設計そのものを変更することでリスクを削減することが目指されます。
- 製造および組立段階:設計された安全策が適切に実装されているか、リスクが新たに発生していないかを確認します。
- 据付および調整:機械の据付や現場での調整中に発生するリスクを評価し、安全な据付手順を確立します。
- 運転段階:日常の使用中に発生する可能性があるリスクを再評価し、安全な操作手順をマニュアルに示します。
- 保守および修理:保守作業中のリスクを評価し、安全な保守手順を策定します。
- 廃棄段階:廃棄時に発生するリスクについても評価し、特に有害な物質を含む部品の処理方法について考慮します。
5. ユーザーインターフェースと緊急停止装置
ISO 12100は、ユーザーインターフェース(UI)の設計にも重点を置いています。操作パネルは直感的で誤操作を防ぐ設計が必要です。また、緊急停止装置の設置も重要で、緊急時には迅速に機械を停止できるようにすることが求められます。
5.1.ユーザーインターフェースの設計
ISO 12100では、ユーザーインターフェースの設計が使用者の安全を確保するための重要な要素として位置づけられています。機械の操作においては、直感的で誤解が生じにくい操作パネルや表示が求められ、これにより使用者が正確かつ安全に操作できることが目的です。具体的には以下の点が重要とされています:
- 直感的な操作:操作ボタンやスイッチの配置は、機械の機能を分かりやすく反映しているべきです。
- 視覚的および聴覚的なフィードバック:使用者が操作の結果を即座に認識できるようにする必要があります。
- 誤操作の防止:ユーザーインターフェースは誤操作を防ぐ設計が必要であり、操作の意図が明確に反映されるべきです。これには、重要な操作に対する確認プロセスの追加などが含まれます。
ISO 12100は、ユーザーインターフェースの適切な設計が、操作ミスや不適切な動作を未然に防ぎ、使用者のリスクを低減するための手段であると述べています。
5.2.緊急停止装置の設置
ISO 12100では、緊急停止装置の設置を機械の安全確保のための基本的な要件としています。緊急停止装置は、機械が異常な状態に陥った場合や危険が差し迫ったときに、速やかに機械の動作を停止させるために使用されます。以下の点が重視されています:
- 速やかなアクセス性:緊急停止装置は、使用者が容易に操作できる位置に設置されるべきです。これは、非常時に迅速に機械を停止させるために必要です。
- 明確な識別:緊急停止装置は他の操作装置とは異なる形状や色(通常は赤色)で設計され、明確に識別できるようにします。
- リセット手順:緊急停止が解除された後に、機械が再稼働する際には安全な手順に従う必要があります。このため、緊急停止のリセットには意図的な操作が必要となります。
ISO 12100は、緊急停止装置を用いることがリスクを低減するための安全措置の一つとして、必須要件であると強調しています。緊急停止装置の適切な配置と設計により、重大な事故の発生を防ぐための重要な役割を果たします。
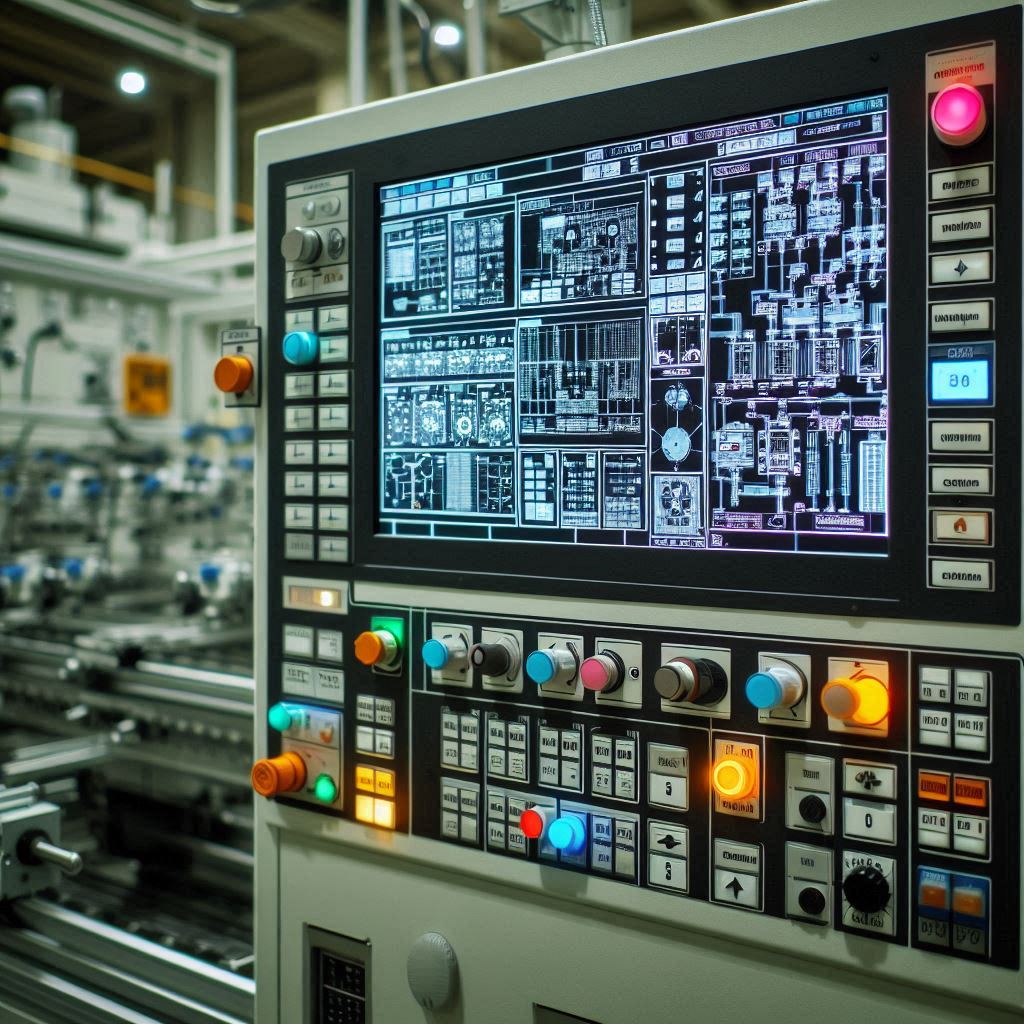
6. 文書化と継続的改善
ISO 12100では、リスクアセスメントの結果やリスク低減策の詳細を文書化することが義務付けられています。これにより、関係者が安全対策の有効性を確認しやすくなります。文書には、危険源の特定、リスク評価、講じた低減措置の詳細、および残存リスクに関する情報が含まれます。また、規格は継続的な改善を推奨しており、技術の進歩や新たなリスクが発生した場合に備えて安全対策を更新することが求められます。
7. まとめ
機械設計者がISO 12100を理解することは、機械の安全性を確保するために非常に重要です。この規格は、リスクアセスメントの手順とリスク低減策を体系的に示しており、設計段階から安全対策を考慮するための基本的なガイドラインとなっています。設計者はこれを活用することで、潜在的な危険源を適切に特定し、必要な対策を講じることができ、事故防止や使用者の安全確保につながります。また、法規制への適合や市場での信頼性向上も期待できます。